How Truck Fleets are Coping With Parts Shortages
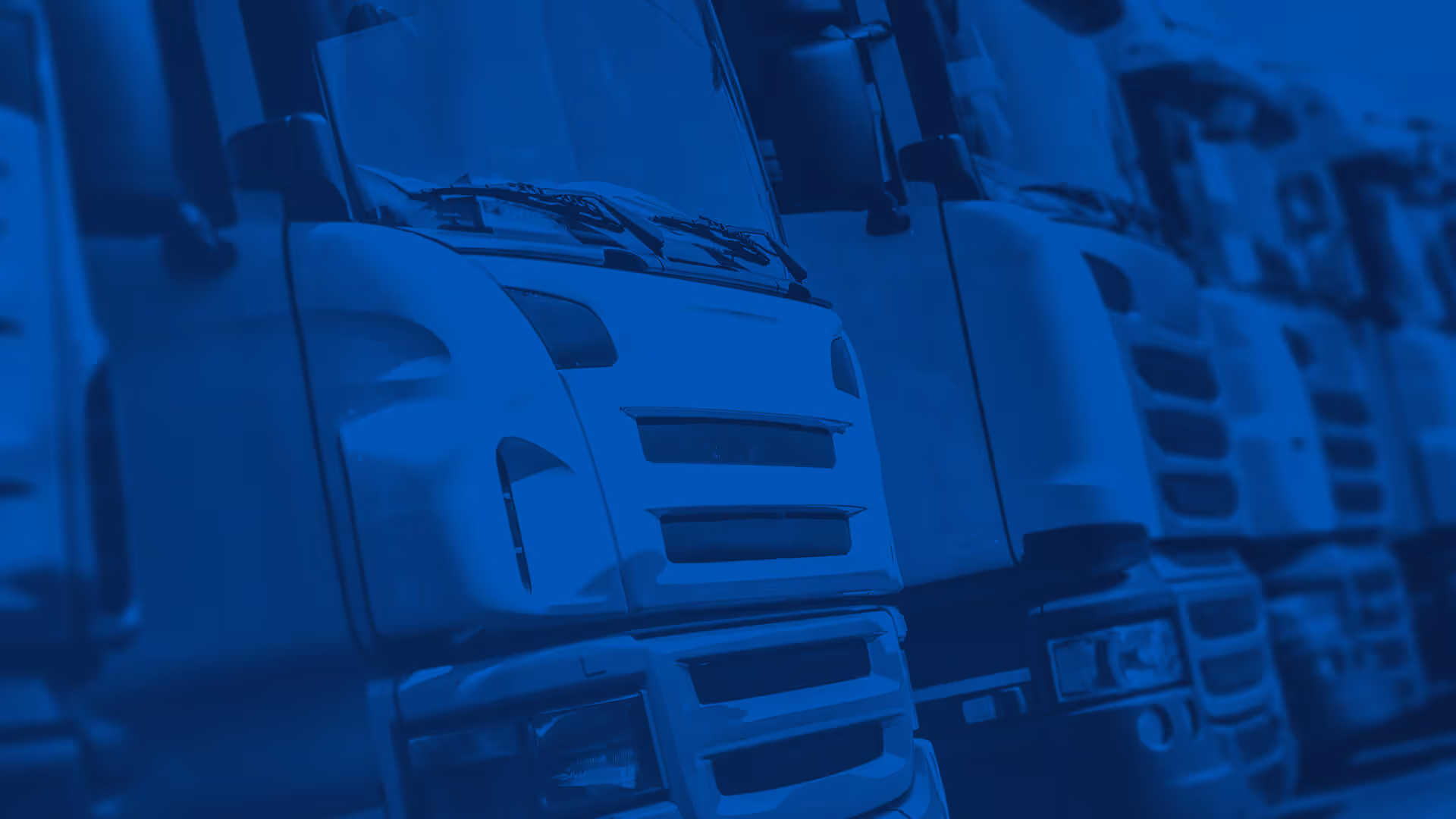
A shortage of truck parts has struck the industry’s spine sending many fleets on a rough roll. Several notable factors have contributed to the turmoil, including the hard-to-forget COVID-19 pandemic. The outbreak has hugely disrupted parts manufacturing patterns and flows, putting stress on the supply chain.
At the same time, manufacturers are dealing with unprecedented semiconductors and labor shortages and thus cannot nearly satisfy the high freight demand in the industry.
The impact on truck parts is widespread. All truck parts have been affected, from tires to windshield wipers to batteries. The volatility of rubber and steel prices has significantly affected the lead times and availability of various items like tires and blocks. Purchase orders take ridiculously long to fulfill, dragging operations by miles.
Irrespective of all these hindrances, the trucking industry needs to keep vehicles on the road and at total capacity.
So, how are they surviving?
In a bid to adjust to the harsh precedents, most of them have gone all out on technology to minimize disruptions from the parts shortage, while others deploy unconventional means to try and survive. Let's look into some of the ways truck fleets are coping with the parts shortage in the supply chain.
Stocking heavily on regularly used equipment
Impulse buying is not always the best financial decision, but where it is justifiable, well— it's considerable. As truck fleets look to safeguard their operations from foreseen downtimes, they purchase essential equipment in large volumes than usual.
These companies are expanding their inventories to accommodate additional purchases of essential items predicted or seem to hit a dearth. Companies are relying heavily on directives from their trusted OEM dealers and representatives for equipment availability alerts to make more informed purchase decisions.
Since the suppliers are more exposed to the market, they can foresee an impending parts scarcity and timely advice fleets on the best measures. Such close communications are calling for great efforts from fleets, to establish a healthy relationship with the dealers. In return, the dealer makes the fleet a priority, constantly availing such crucial market information to them.
In addition, firms are immediately restocking parts that have been used in repairs— making sure their stocks are always fully packed.
Venturing into secondary sources of parts
Shortage in supply of essential parts through the mainstream OEMs has seen fleets go out of the book searching for supplemental sources of parts to keep them running.
Some fleets have been pushed to dive into online stores such as eBay and Amazon to scoop out the parts they can find— new or old. Others have dismantled their trucks to leverage every valuable part they can get.
On multiple occasions, fleets have sent their representatives on a wild hunt for spare parts in local retails— a vehemently rare occurrence in the past few years.
Cost seems to be a secondary concern for most fleets, considering that retail prices are always much higher than the usual load purchase prices, but do they have a choice?
Streamlining communications for quick and timely repairs
Fleets have gone on an innovation spree to design above-the-fold information sharing systems for quick attendance to broken-down trucks. These systems include, among others, in-house designed software which can detect failures in a truck and alert the driver immediately— even on transit.
These softwares also send signals to the fleet’s repair team and directs them to the truck's exact location. These prompt response systems are being adopted to maintain top customer service by avoiding delays by all means. The truck driver does not have to go through multiple reporting channels to repair a broken truck.
More importantly, fleets are continuously streamlining communications with service providers by openly discussing the estimated wait times whenever there is a breakdown. These communication measures play a crucial part in maintaining customer relations and keeping service providers on their toes to act with speed.
Further, fleets are laying down protocols to smoothen authentication of payments to vendors. They reduce the verification steps required to purchase required items to cut down on time taken in repairs. In addition, the adoption of more convenient communication software such as Microsoft Teams and Zoom is significantly improving communications between workforces. Workers can effectively consult and guide each other in technical operations, cutting down on phone calls— which are less convenient in most technical consultations.
Investing heavily in VMRS coding systems
Vehicle Maintenance Reporting Standards (VMRS) is a standard created by the American Trucking Associations (ATA) to identify components, parts, and labor for vehicle maintenance. VMRS assigns alphanumeric codes to every aspect of the trucking industry: from the engine and transmission to tires, brakes, and axles. Trucking companies rely on these codes more than ever to track the cost of maintenance and minimize the time taken to diagnose a problem.
With the thousands of possible VMRS codes, technicians can quickly diagnose problems with specific parts on vehicles and schedule a repair before the fault becomes rampant.
These timely detections of faults and consequent repairs are helping truck fleets avoid costly breakdowns, which would otherwise occur, lest the timely intervention. Further, the detection codes are incredibly smoothing operations, as fleets use the data available to plan for repairs without much urgency.
They have enough time to go out and look for the required parts for the repairs, or even take the necessary measures to control damage rates and increase a part’s service duration.
Final thoughts
Despite the unfavourable operational conditions in the trucking industry, fleets are finding sustainable ways to maintain their highly-demanded services. By staying informed on the supply trends, anticipating breakdowns, and timely responding to failures, fleets can maintain good order of operations, minimizing downtimes as much as they can.
As many hope for the crisis to ease over time, it's hard to tell how long the parts shortage will go. Fortunately, supplies seem to get back on track slowly, with the world gradually recovering from the wrath of the pandemic. It is therefore a wait and see situation, on how the situation will turn out as the year unfolds.
Read our TMS Buyer's Guide
Navigate the TMS software landscape with our comprehensive buyer's guide - find the perfect platform for your trucking business today.
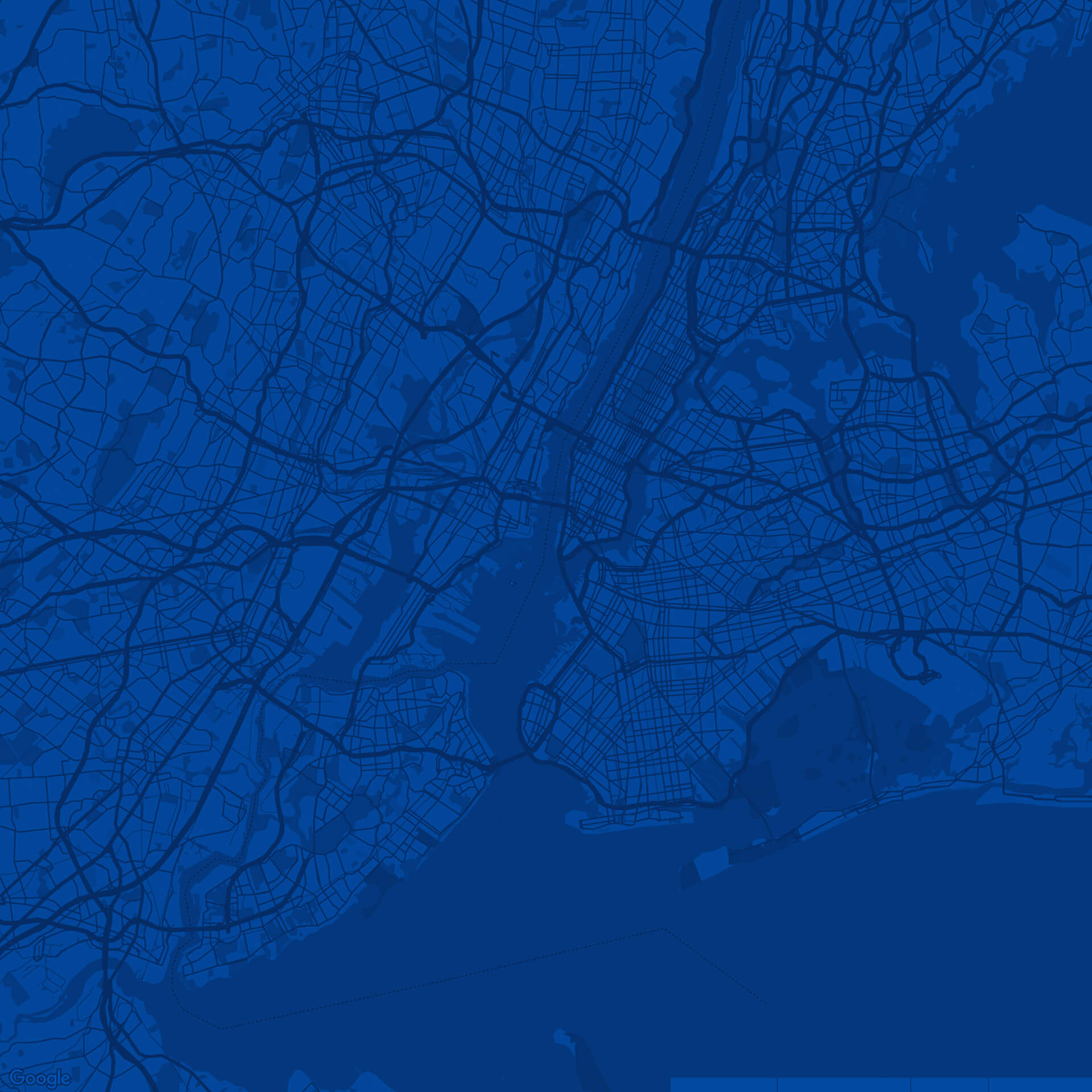
Latest From the Blog
Our Insights on Tech, Industry Trends, and News.
%20Reduces%20Shipping%20Times%201920x1080_c.jpg)
How Transportation Management Software (TMS) Reduces Shipping Times
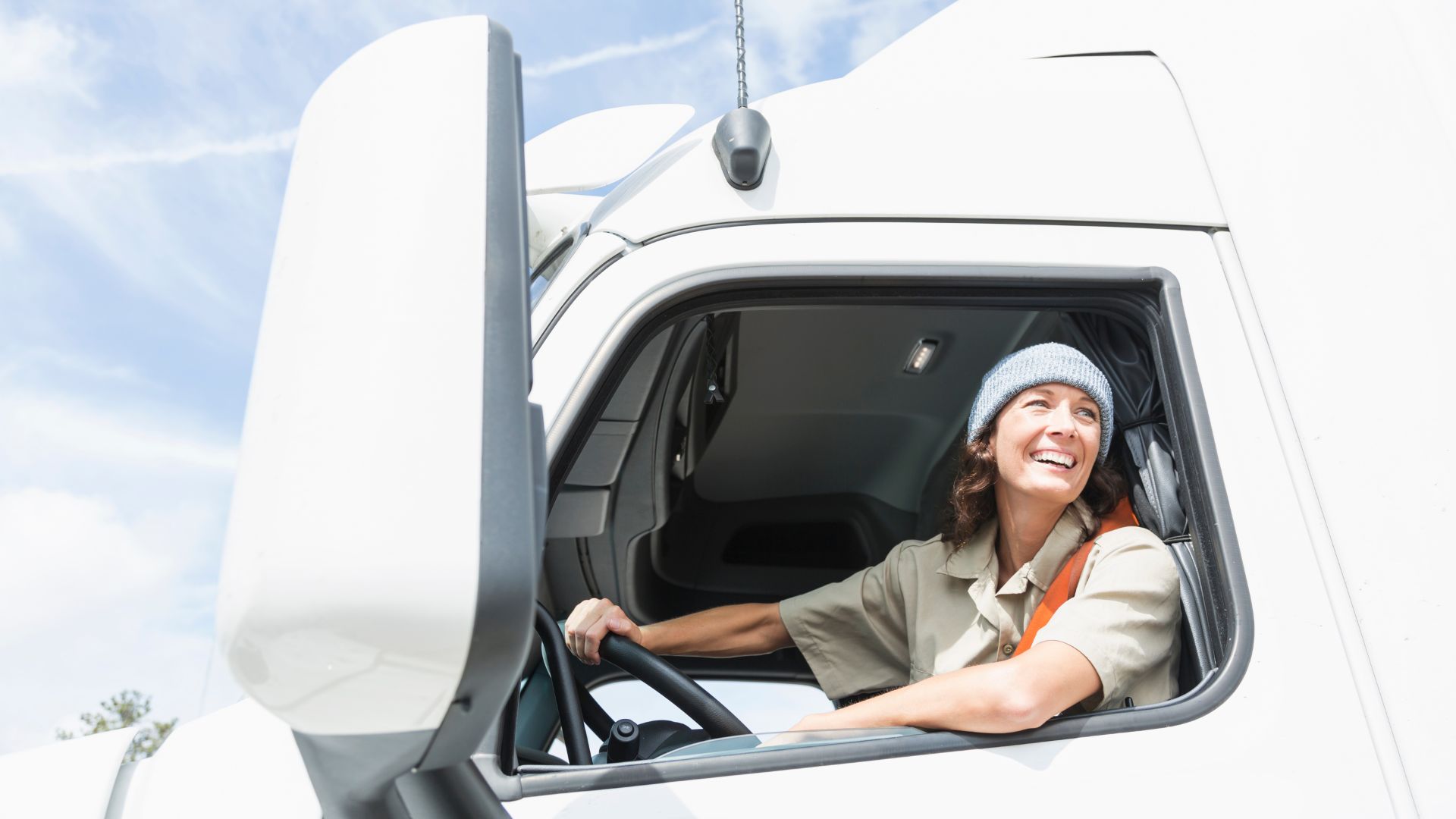
How Does a TMS Improve Logistics Management?
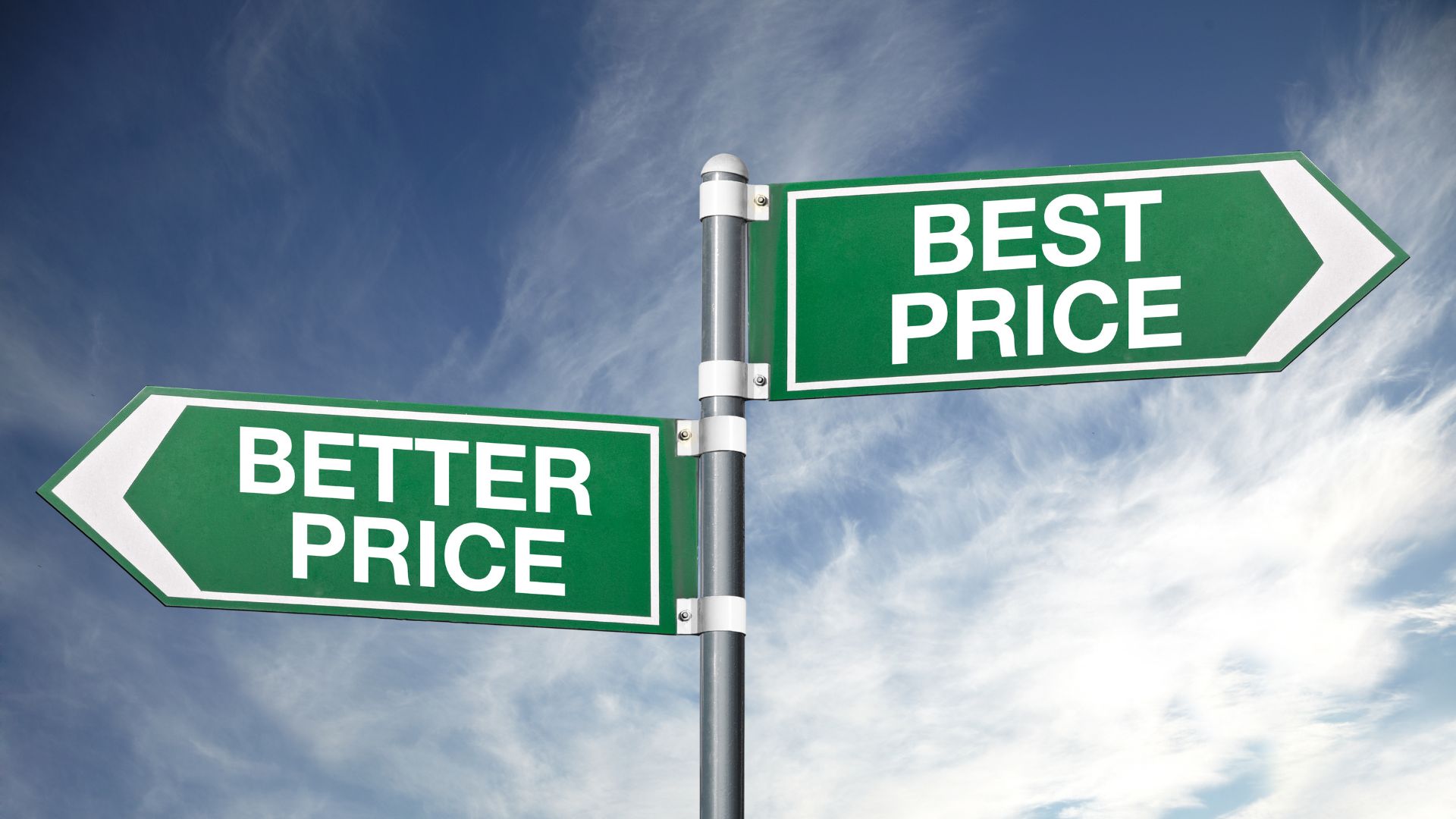